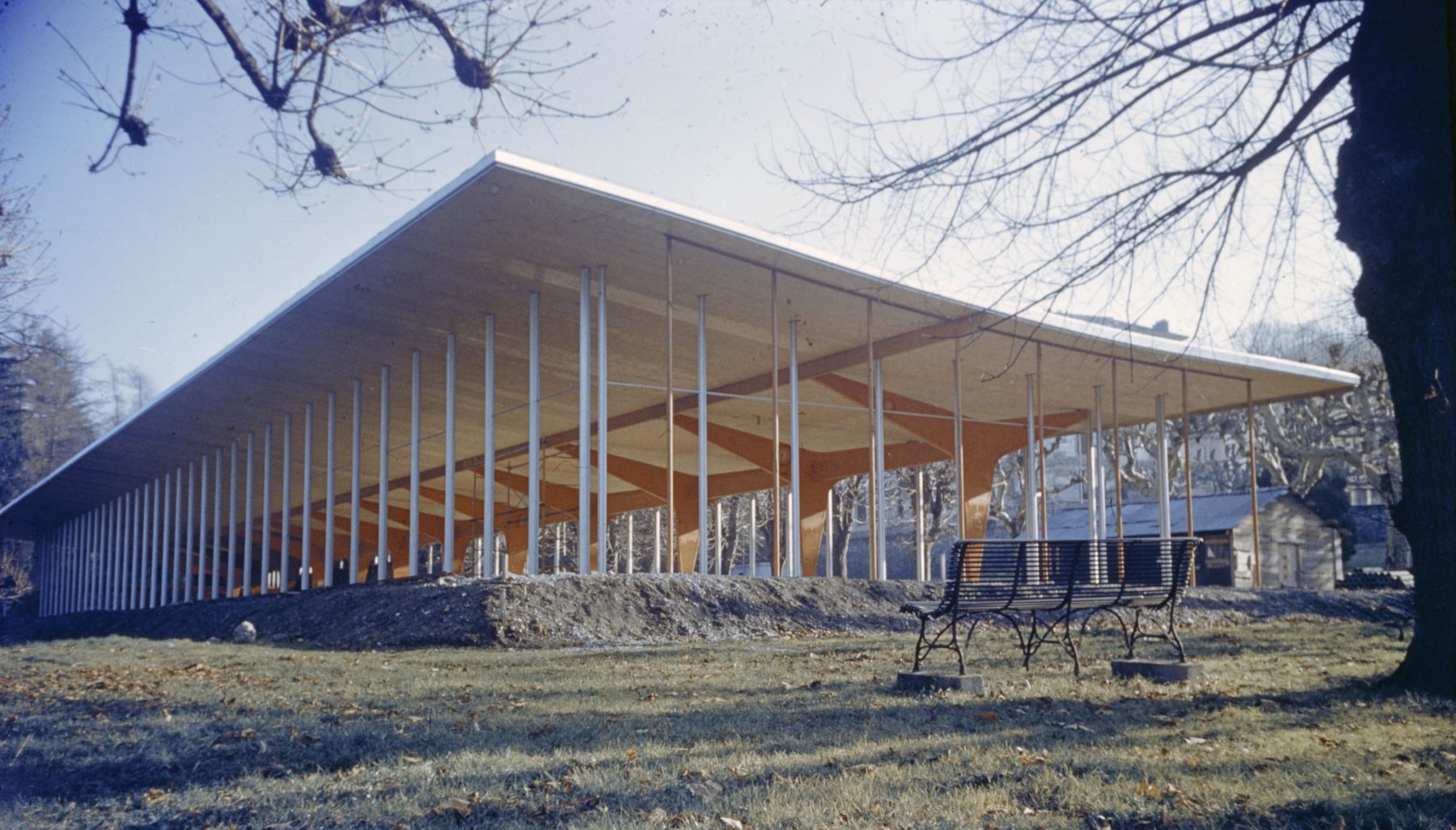
The Windows of the Cachat Buvette in Evian|Jean Prouvé’s Windows #4
18 Jul 2024
After resuming his creative activities with his new firm, Jean Prouvé Constructions, Prouvé presented an alternative version of the béquille in a project he had been working on concurrently with the Villejuif Temporary School, where he first brought the structural system to realization. The fourth installment of Jean Prouvé’s Windows discusses the window designs of the Cachat Buvette in Evian (1957).
The Cachat Buvette in Evian
In November 1955, architect Maurice Novarina1 visited Jean Prouvé, who had been reassigned to Paris, to informally recruit him as a collaborator on the Cachat Buvette in Evian (Buvette de la Source Cachat, Évian), a building planned within a newly created mineral springs park on the French shore of Lake Geneva. Prouvé initially bid for the project as the “Prouvé Group”, but officially took it on with his firm Jean Prouvé Constructions. He began working on this project before the Villejuif Temporary School (1957), though the latter was completed first. Société Goumy handled the construction work, and Serge Kétoff2 performed the structural calculations.
The rectangular building, measuring 78.75 meters by 14 meters, is a single-story structure with a basement and a structurally independent mezzanine level. Its plan is composed on a square grid with a basic 2-meter module, and the mullions along the perimeter are placed every 2 meters to align with the grid. The row of round steel columns at the west end of the building are remnants of an unrealized vision to create a semi-outdoor gallery; they were intended to be equipped with original Prouvé-designed aluminum sunshades. The spaces are divided into four zones: a drinking space, a lounging space, a music hall, and a mezzanine gallery. The original plan included restrooms and a small shop on the basement level, as well as an outdoor terrace on the ground floor.
Comparable to a Japanese balneotherapy spa (tōjiba), the building was built as a facility to promote the health benefits of Evian mineral spring water. Visitors could drink the water while relaxing in the indoor and outdoor lounging spaces. Additional entertainment was provided in the music hall, where orchestra performances were held twice daily during the peak season. Visitors could enjoy all of these amenities for free.
The facility opened its doors in May 1957. As it was intended for use only during the warm season, it was intentionally not designed with the specifications necessary for creating a comfortable indoor environment during the cold season, such as airtightness and insulation. In 1986, it was designated as a historic landmark; however, the mezzanine gallery and its access stairs have since been removed, and it has been partially renovated to connect with a new structure built to the east. Nonetheless, the building is one of the very few surviving Prouvé projects still in use today, and the original wall mosaic artwork by Raoul Ubac3 and André Beaudin4 also remain intact.
-
© Claudio Merlini, Geneva.
Window Designs Made from Two Components
The Cachat Buvette in Evian has a variety of design features familiar from other Prouvé projects. Its roof is sheathed with sheet aluminum and backed by hard fiberboard (Isol) and Rousseau ceiling panels, consistent with the specifications employed since the Prouvé House. In fact, the sheet aluminum was being sold as Jean Prouvé roofing (bacs de toiture Jean Prouvé) by the time of this project. Ironically, however, the product only became known across France after Studal relinquished Prouvé of his patents and rebranded it as Triondal, removing its creator’s name to enhance its international marketability.
Similar to the Villejuif Temporary School, this building has a transparent glass-encased interior that provides 360-degree views of the surroundings. The glazing on all but the south façade is also divided into two sections, again by utilizing the same I-section horizontal glazing bars (extruded aluminum) from the Prouvé House. The lower lites have a uniform height of 3.45 meters, while the upper lites are angled along the top to conform to the bowed shape of the roof on the east and west sides. These angled lites elegantly bridge the 1-meter height differential between the south side (4.25 meters tall) and north side (5.25 meters tall).
-
© Claudio Merlini, Geneva.
The glazing used is basic 6-millimeter-thick clear glass, and the window headers have deliberately been omitted. As a result, the wooden ceiling seems to visually swoop towards the sky, directing one’s attention to the scenery beyond the lake-facing north windows. Contributing to this effect are eight sliding glass doors that measure 2 meters by 5.25 meters, matching the pitch of the mullions and the height of the fixed glazing. Each of these doors is equipped with two wheels that enable them to be slid sideways along rails in the floor. Looking at the floor, one can see that the randomly placed slate flooring stones (ardoise) create a continuous texture across the interior and exterior spaces, which seem to merge into one when the enormous sliding doors are opened. On the south side, or the rear façade, there are two tunnel-like entrance vestibules constructed from bolted pieces of folded thin aluminum plate, fitted with two layers of frameless double-swing glass doors. This vestibule design was repurposed from the French Petroleum Institute (Institut Français du Pétrole, 1958), a project which Prouvé designed and built during the same period.
The façade mullions are formed from pairs of joined extruded aluminum profiles. These profiles were fabricated using casting molds produced for the Aluminum Centenary Pavilion (Pavillon du Centenaire de l’Aluminium), which Prouvé worked on during his reassignment in Paris.5
The difference with the mullions of the Cachat Buvette is that they have been improved to allow steel end plates to be slotted into them and fastened with bolts, eliminating the need to cast separate aluminum base and cap components. While the profiles used to make them appear to have symmetrically shaped cross sections in the floor plans, closer inspection will reveal differences in the shapes of the tongues and grooves along their joining faces. These asymmetries allow a 125-millimeter-deep profile (hereinafter referred to as “125 profiles”) to interlock with another profile of the same type flipped upside down, thereby forming a single element made of two identical components. The 55-millimeter-deep profiles (“55 profiles”) feature these same details, allowing for the creation of three types of differently shaped elements by pairing of two 125 profiles (“125+125 profiles”), a 125 profile and a 55 profile (“125+55 profiles”), and two 55 profiles (“55+55 profiles”). 125+55 profiles line the north and south façades, serving as columns for supporting the roof, while 55+55 profiles are used for the west façade mullions, which do not bear axial loads. 125+125 profiles were used in the Aluminum Centenary Pavilion, but not in this project.
The façade glazing rests atop a gasketed L-shaped sill angle on the interior side and is held in place by gasketed glazing brackets at three points along both the bottom (floor end) and top (ceiling end). Vertically, the glazing is lined with indoor gaskets (Joint Hélios; extruded waterproof silicone rubber) and held in place by outdoor glazing clamps fastened to the tongues of the mullion profiles. These details, which are the same for the glazing fitted to both the 125+55 profiles and 55+55 profiles, result in creating a gap of about 10 millimeters between the glazing and ceiling. As I will discuss later, this “gap”, which is plugged by a V-shaped gasket (extruded silicone rubber), is in fact the most crucial design feature of this building’s windows.
The Structures that Coexist with Prouvé’s Windows: The Béquille—Part II
This building features 13 of Prouvé’s asymmetrical, T-shaped “béquilles“, painted white and arranged in a line at intervals of 6 meters (three spans of the 2-meter modules).6 Although slightly different in form from those of the Villejuif Temporary School, their outer shells are also made with folded sheet steel, which here has a thickness of 5 millimeters. Their internal steel channels have also been replaced with I-profiles for increased strength. Notably, the area where the two cantilevering arms meet (the central part of béquilles) has been enlarged. While appearing seemingly overstructured, the added rigidity ensures that the béquilles do not deform by tilting forward under their own weight as they did at the Villejuif Temporary School. Consequently, the north columns also have no need to be slanted and are designed as vertical posts.
Another distinctive feature of these béquilles is that their central column members do not touch the roof, and the tips of their cantilevering beam members appear to be pulling the roof downward rather than pushing it upwards. At its back lower end (south end), the roof is equipped with a rain gutter that blends seamlessly into the thickness of the roof, while at its front upper end (north end), the sheet aluminum roofing wraps down over the eaves and is tapered. Both details accentuate the roof’s thinness.
Furthermore, as this building is larger than the previous examples discussed, the longitudinal beam with a V-shaped cross section fixed to the front tips of the béquilles plays a much greater role. Here, the beam is not merely a tie beam serving to bear lateral forces; rather, its purpose is to support the roof. In other words, the V-shaped beam serves to distribute the stresses of the roof spanning between adjacent béquilles across three support points, much like how the stresses of the spans supported by each béquille cross-sectionally are also divided into three.
-
(C) Centre Pompidou, MNAM-CCI Bibliothèque Kandinsky, Dist. GrandPalaisRmn / Fonds Prouvé / distributed by AMF
One point still requires explanation: why the aluminum mullions were divided into two components in the first place. While doing so allowed for the reuse of the casting molds from the Aluminum Centenary Pavilion and enabled the creation of columns with various cross sections, such fabrication matters were not the reason. The Prouvé we are familiar with certainly would have designed the mullions aligned with the béquilles as tension members for stabilizing the béquilles and designed the mullions between the béquilles as columns for supporting the roof, treating both as primary structural elements tailored to address the different types of stresses.
And in fact, if you look at images of the easternmost end of the building from the time of its completion, you will find one asymmetrical béquille standing in its pure form, clearly balanced with the help of a steel tie rod instead of an aluminum support. As I explained in the article on the Villejuif Temporary School, the béquille was conceived to work in tandem with a tension element affixed to its shorter beam member. In a rare instance among Prouvé’s designs, where multiple functions are often superimposed onto a single element, this steel tie rod exists purely as a primary structural element with no additional functions.
The rationale for using two-component mullions can be explained by understanding the varying structural potentials that materials have based on their properties. For example, steel has approximately 1.5 times the tensile strength of aluminum. This means that steel demonstrates a broader range of elastic deformation (the extent to which it can endure stress without permanently deforming). It is easy to imagine that Ketoff, the structural engineer, determined that aluminum could not be used for the tension members, which are critical to the integrity of the béquille structural system—as is evident from the fact that he revised the diameter of the steel tie rods, initially designed at 20 millimeters, to 30 millimeters in the final design. The need to use two kinds of metals based on their respective structural properties—steel for the tension members and aluminum for the compression members—was what led to the solution of separating the hollow aluminum columns into two components and enclosing (concealing) the steel tie rods within them.
Yet, this solution presented another issue: compared to steel, aluminum expands about twice as much in the summer and contracts about the same amount in the winter. Evian experiences a significant annual temperature fluctuation, with summer highs reaching up to 35 degrees Celsius and winter lows dropping to -5 degrees. Using aluminum mullions meant that the building would expand and contract vertically by about 5 millimeters, so the windows had to be designed with sufficient clearance to accommodate this movement. Solving this issue necessitated omitting the headers to create that crucial “loose-fitting” detail along the top of the façade, ensuring that the glazing does not crack due to the building’s seasonal movements.
-
(C) Centre Pompidou, MNAM-CCI Bibliothèque Kandinsky, Dist. GrandPalaisRmn / Fonds Prouvé / distributed by AMF
The Evolution of Prouvé’s Gravity-Defying Windows
What Prouvé unlocked by leveraging the elastic properties of Rousseau panels in the design of the Prouvé House was the possibility to create seemingly gravity-defying sinuous (multi-curved) roof designs characterized by their thinness relative to their long spans and ease of construction. Like those used in the previous projects, the Rousseau panels of the Cachat Buvette have been formed into units, which measure 0.75 meters in width and 19 meters in length. However, these panels are the thinnest yet at 26 millimeters, as they are not structural components. The distance between the mullions of the front façade (north side) and the front tips of the béquilles is approximately 6 meters, or nearly twice as long as the spans of the earlier projects designed with Rousseau panels. Prouvé undoubtedly would have been aware that the Rousseau panels alone clearly could not bear the weight and wind-induced in-plane stresses of the roof.
Naturally, there must exist an “invisible” frame somewhere here. Fixed to the Rousseau panels at intervals of 750 millimeters, this unseen frame is made of hybrid wood-and-steel beams (la bordure de rive), each consisting of a wooden beam (180×60) reinforced on both sides with steels plates (PL-45×6) and angles (L-45×45×6). Additional wooden beams, placed longitudinally, prevent the lateral buckling of these 19-meter-long hybrid beams while also serving as the roof’s substructure.
The roof of the Cachat Buvette hence is designed as a structure of lines rather than planes, forming an entirely different type of structural system from that of the earlier projects. Moreover, to create the roof’s curvatures, the workers had to manually force the hybrid beams into shape using a jig matching the roof’s cross-sectional profile, which was prepared on the floor during construction.
The modified roof design presented an additional detail that needed to be resolved. While cantilevering the eaves made rational sense for counterbalancing the stresses in the planar structures, doing so in this linear structure required the introduction of beams for supporting the cantilever. This posed a structural detailing problem at the intersections between the hybrid beams supporting the cantilever and the steel channels (C-100×50×6) connecting the façade mullions longitudinally: the problem of the rigid joint detail.
Ketoff’s early sketches show that he originally intended to solve this problem using hybrid beams configured differently from those of the built design. He had planned to use steel channels (C-100×50×6) for the lower part of the hybrid beams throughout as a general rule, while adding reinforcing (C-80×45×6) to the upper part of the hybrid beams at the inflection points of the bending moments. The beam depth of 180 millimeters was determined based on this plan. He likely decided to employ such hybrid beams because their wooden cores mesh well with the wooden Rousseau panels, enhancing their role as jigs and thus allowing notches to be cut into them at their joints with the intersecting steel channel without major concern.
However, the hybrid beams were later reconfigured with steel plates and angles, presumably because the channels, being as rigid as they are, could not be bent to form the desired curves. This necessitated the steel-to-steel joints to ultimately be welded on site. And so, despite its outward resemblance to past projects, the Cachat Buvette was constructed using entirely different structural solutions that rendered it a building that cannot be disassembled and relocated. Nonetheless, this non-dismountable structure gave rise to unique frameless window details, resulting in a space imbued with an unprecedented sense of synergy. Or, put differently, this architectural creation, with its views to Lake Geneva as Novarina envisioned and the art pieces by Ubac and Beaudin integrated into its floor, stands out within Prouvé’s body of work as an unusually vernacular project.
Notes
1:Maurice Novarina (1907–2002): French architect. He envisioned creating a fully glazed, steel-framed building with a rectangular plan orientated towards Lake Geneva from the start. The similarity of this scheme and Prouvé’s earlier designs made their collaboration inevitable.
2:Serge Ketoff (1918–2005): Engineer. He produced the structural calculations for the béquilles and roof.
3:Raoul Ubac (1910–1985): French painter, sculptor, and photographer.
4:André Beaudin (1896–1979): French painter and sculptor.
5:Built in the summer of 1954 along Paris’ Quai Branly on the bank of the Seine, the pavilion was designed to commemorate the centenary of the discovery of aluminum. It featured taller mullions made with 125+125 profiles and shorter mullions made with 125+55 profiles. In the following year, the building was repurposed to host an international conference organized by the Society of Mineral Industry (Société de l’industrie minérale), also to mark its centennial. It continued to be used until the summer of 1955, but was dismantled around March 1956 with no further plans for reuse. As this coincided exactly with the commencement of construction on the Cachat Buvette, there is a theory that some of the pavilion’s 125 profiles and 55 profiles were reused at Evian. According to this theory, some of the profiles had their cast aluminum end caps removed, were unwelded (sliced), and then rejoined on site with bolts. However, I describe the profiles as having been recast because I concluded from my investigations that the pavilion’s mullions were composed solely of 125+125 profiles and no 55 profiles were used elsewhere in the project. Moreover, aside from the those enclosing the steel tie rods, none of the Cachat Buvette’s profiles had to be joined to each other using bolts. Today, the pavilion can be found at the Paris Nord Villepinte, where it was relocated and renovated. It was designated as a historic monument of France in 1993.
6: The actual béquilles used were manufactured not by Société Goumy but by Fanara, a company based in the Paris suburb of Bagnolet. Due to transportation constraints, Société Goumy decided to produce the upper and lower parts of the béquilles separately and weld them together on site using connectors.
References
“Buvette de la source Cachat, Évian”, L’Architecture d’Aujourd’hui, no. 75 (1957): 52–53.
Franz Graf and Giulia Marino, La buvette d’Évian: Maurice Novarina, Jean Prouvé, Serge Ketoff (Infolio, 2019).
Peter Sulzer, Jean Prouvé: Complete Works: Volume 4: 1954–1984 (Birkhäuser, 2008).
Bruno Reichlin et al., eds., Jean Prouvé (Tokyo: TOTO Publishing, 2004).
Jean Prouvé, Builder of Design, trans. Reiko Hayama (Misuzu Publishing, 2020).
Top image: (C) Centre Pompidou, MNAM-CCI Bibliothèque Kandinsky, Dist. GrandPalaisRmn / Fonds Prouvé / distributed by AMF
Shin Yokoo
Founded Ouvi in 2004 after completing a masterʼs degree in architecture at the Tokai University Graduate School of Engineering and working at the Masahiro Ikeda Architecture Studio. Earned a PhD (Engineering) from the Tokyo University of Science Graduate School of Science and Technology in 2016. Special lecturer at the University of Belgrade from 2017 to 2019 (one-year trainee of the Agency for Cultural Affairsʼ overseas study program). Visiting senior fellow at the National University of Singapore since 2020, Senior Lecturer from 2022. Visiting associate professor at the Tokyo University of Science from 2022. Notable works include the Matsumoto Sannomaru Square (2023; designed by Tatsuo Iwaoka Laboratory + MORIIS ATELIER), the MNH (2023; designed by ICU), the House in Nakago (2021; collaboration with Snark), 4 Episodes (2014; Atelier Nishikata), and Jukkaie (2009; collaboration with Point). Notable research includes “Design Feature of ʻMaison du Peuple de Clichyʼ Designed by E. Beaudouin, M. Lods, J. Prouvé”, (AIJ Journal of Technology and Design, Jun. 2015), “Study on the Relationship Between Features and Building Components of ʻAéro-Club Roland-Garros à Bucʼ” (AIJ Journal of Architecture and Planning, Jun. 2015), and “Study on the Relationship between Features and Building Components of ʻMaison démontable en ancier BLPSʼ” (AIJ Journal of Architecture and Planning, Sep. 2017), among others.
