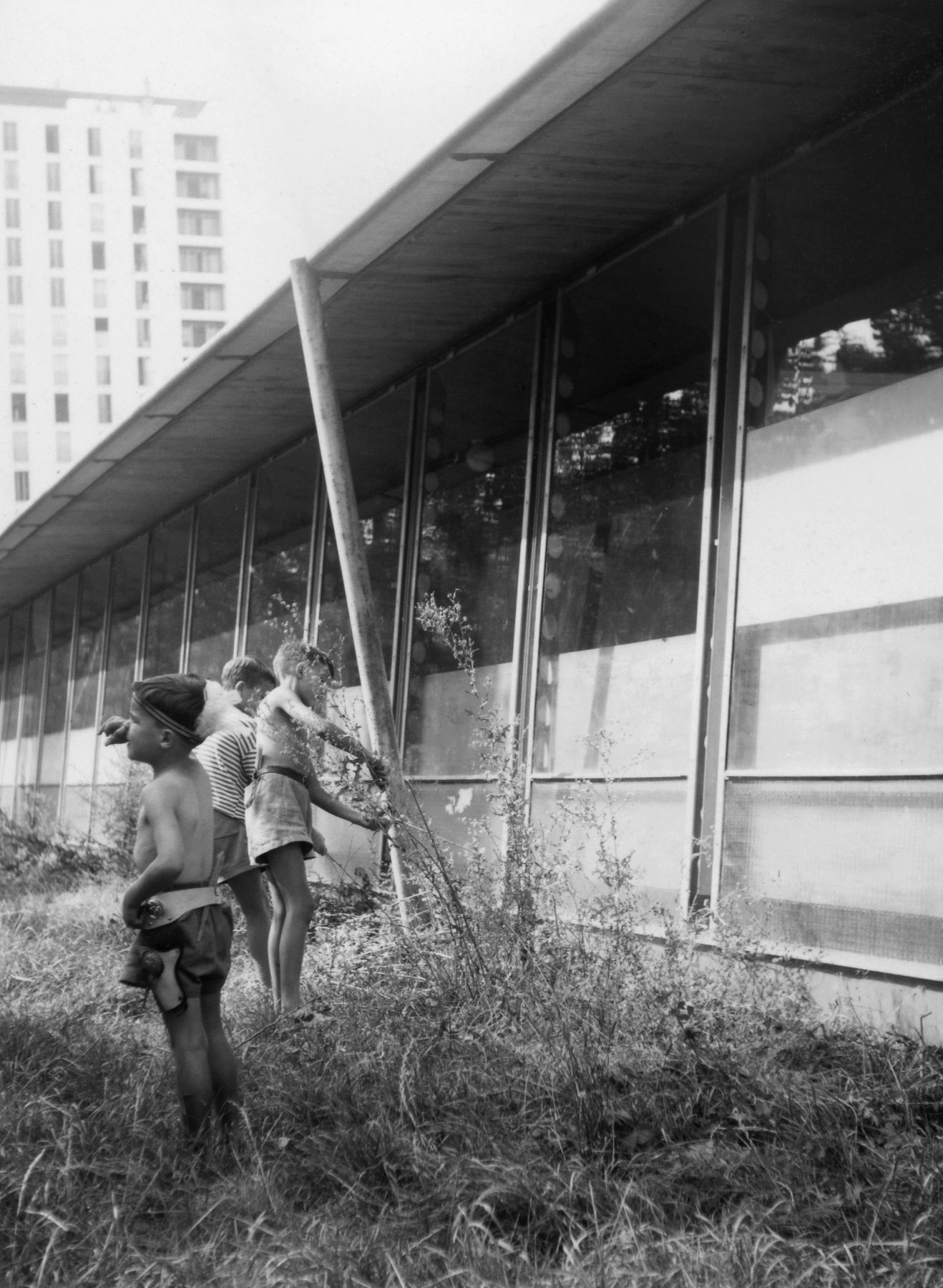
Windows of the Villejuif Temporary School|Jean Prouvé’s Windows #3
28 Mar 2024
After being driven out of the Maxéville Factory in Nancy, Prouvé was prepared to go into retirement at his self-built home. Yet, he would begin developing new window designs again after reuniting with a certain friend. The third installment of “Jean Prouvé’s Windows” looks at the window designs of the Villejuif Temporary School (1957).
Jean Prouvé Constructions
In 1954, L’Aluminium Français, the parent company of Studal, relegated Prouvé to its office building on Avenue Kléber in Paris. What was Prouvé to do with himself after having been stripped of his workshop and forbidden to use the fifteen patents he had acquired over the years for his own designs? Reflecting on the moment, he likened the experience to being confined in a Gestapo bunker (the former headquarters of which were visible from the office’s windows). It was during this time that he reconnected with his friend Michel Bataille, whose encouragement helped him find the resolve to move forward by coming to terms with his past and setting himself free. In January 1956, two years after completing the Prouvé House (1954), Prouvé agreed to a settlement deal with L’Aluminium Français. The terms included renaming the Maxéville Factory and transferring all his workers and previously acquired patents to the company. In return, he received compensation, which he used to found Jean Prouvé Constructions (Les Constructions Jean Prouvé) together with Bataille. The launch of this new technical design firm in a small Paris apartment on Rue Léon-Jouhaux in May 1956 marked the beginning of the second chapter in Prouvé’s life.
-
Prouvé (third from right) with members of Jean Prouvé Constructions.
© ADAGP, Paris & JASPER, Tokyo, 2024 E5493
The Villejuif Temporary School
Shortly after founding his firm, Prouvé was commissioned by the City of Villejuif to construct the Villejuif Temporary School (École Provisoire, Villejuif). This was an elementary school intended for the children of 1,500 families expected to move into the city as Paris’ population rapidly expanded into the suburbs. Its buildings were required to be designed as a lightweight, economical modular system that not only could be quickly assembled but also could be disassembled for reuse as a summer camp facility. Prouvé likely would have viewed this order for easily assemblable and disassemblable buildings as an ideal project for restarting his career.
Design work on the buildings was started right away in 1956, and construction was completed around the spring of 1957. The construction work was contracted to Société Goumy, a Paris-based company specializing in steel frame construction, which carried out the fabrication of all the building components in a factory and their assembly on site. The project consisted of a total of three buildings. Two of them, positioned side by side, had footprints of 75.25 meters by 8.75 meters (approx. 630 square meters) and contained seven classrooms and a gallery connected by a single-loaded corridor running along their entire length. The third building, positioned to stand centered on the other two a short distance away to the south, measured slightly smaller at 49.00 meters by 8.75 meters (approx. 430 square meters), and it contained four classrooms and a gallery. The buildings were designed on a grid of 1.75-meter-square modules, as specified by the French Ministry of National Education, and the classrooms and galleries had areas of 61.25 square meters (5×4 grids) and 122.5 square meters (8×5 grids), respectively. The structural elements placed between the corridors and classrooms are referred to as “béquilles” (“crutches”) due to their shape. Serving to support the roofs, these Prouvé-designed structures had a standard spacing of 3.5 meters (two spans of the 1.75-meter modules), with a shorter spacing of 1.75 meters around the classroom entrances. Access to each building was provided on the north side at 17.5-meter intervals (every ten spans of the 1.75-meter modules), such that each entrance was shared by two classrooms.
-
Partial plans
-
Site plan
360-Degree Glazing
Each buildings had a glass curtain wall tilted roughly 10 degrees inwards on its south face and a vertical glass curtain wall on its north face. The east and west faces were also built as vertical glass curtain walls, whose tops were fitted to the curvature of the roof. V-shaped perimeter columns, placed every 1.75 meters in line with the grid, served as the mullions needed for realizing a fully glazed envelope.
-
Elevations
-
Photo (C) Centre Pompidou, MNAM-CCI Bibliothèque Kandinsky, Dist. RMN-Grand Palais / Fonds Prouvé / distributed by AMF
Each V-column was formed from a thin piece of folded sheet steel (3 millimeters thick), and separately made exterior glazing beads (extruded aluminum) were attached along the flanges to conceal the gaskets. Bolts, fastened from the interior side, tied these parts together and fixed the glazing in place. Clear glass was fitted at the top of the windows and wire-reinforced frosted glass was used at the bottom. Inserted between them was a horizontal glazing bar with an I-shaped cross section (extruded aluminum), a detail Prouvé reused from the living room curtain wall of his home. Prouvé designed all these details to allow the various façade components to be freely reconfigured, and like the glazing bars, the V-columns could also be interchanged with the columns/mullions of his living room. Such techniques (details) for enabling simple things to be transformed in diverse ways would recur time and again in his later façade designs.
-
Axonometric drawing of the V-columns -
Axonometric drawing of the façade components
In plan, each standard V-column spread to a width of 275 millimeters on its exterior-facing side, converged to a width of 53 millimeters on its interior-facing side, and had a depth of 141 millimeters. Those used at the corners of the buildings had flanges folded to a different angle from those on the long sides (118 degrees instead of 70 degrees), and those on the north and south faces simply differed in height. Those on the short sides were fabricated from the same ones used on the long sides, but their tops were cut at an angle to match the roof curvature. The flanges of the columns had 120-millimeter-diameter holes cut out from them at 200-millimeter intervals that served not only for weight reduction but also for ventilation. A hinge plate (extruded aluminum) was mounted vertically along the flat inner face of the web to hold ribbed flaps (extruded aluminum), which served as operable shutters for the ventilation windows. These shutters were equipped at the tips with a plastic attachment shaped like a claw in section to seal the gap with the column when the shutters were closed. Additionally, the bolts that held the aluminum hinge plate to the column were designed to secure shelves, wooden cover panels, and other attachments on the interior side. The way this single element incorporated operable mechanisms and multifunctionality is a hallmark of Prouvé design.
-
Details of the V-columns
The ceilings of the classrooms were made with 40-millimeter-thick standardized long-span pressure-laminated wood panels known as Rousseau panels (panneaux Rousseau), fitted to form a smooth surface with inconspicuous joints. These panels were backed with beaverboard (isorel mou) for sound and thermal insulation, and covered above by sheet aluminum roofing. The roofs projected about 1 meter beyond the south faces of the buildings to meet solar radiation standards and provide necessary shade for the classrooms. The classrooms would have been well lit with their ceilings set at a height of around 3 meters throughout. With three of their sides glazed, those on the east ends especially would likely not have needed lighting fixtures during the day.
The partition walls between the classrooms were made of flax chipboard panels (Linex panneaux), which were layered for enhanced soundproofing. The same 40-millimeter Rousseau panels as those used on the ceilings were utilized for the partition walls between the classrooms and galleries due to their fire resistance capabilities. Since both types of wall panels were linked together with wood-to-wood joints, they could stand simply by being bolted to the floor and ceiling without the need for studs. The structural members at the wall terminations were detailed with slots to receive the end panels, allowing for dry construction and preventing the creation of gaps between the different materials. Shelves, oriented perpendicularly to these walls, spanned between the béquilles, separating the classrooms from the corridors. The gaps above and below the shelves were fitted with sliding glazing panels and Rousseau panels, respectively.
-
© Photo : Lucien Hervé, Paris
The Structures that Coexist with Prouvé’s Windows: The Béquille—Part I
The béquilles supporting the roofs were each composed of a column member and a beam member. The column member was made from two pieces of thin sheet steel (3 millimeters thick) that were folded into C-shaped sections and wrapped around a core comprising two steel channels (2C-100×50) aligned face to face. Similarly, the beam member was formed from pieces of thin sheet steel (3 millimeters thick) folded into C-shaped sections and clamped around the column member. The two parts were connected by bolts inserted at the four corners of their overlapping area. Despite having the initial appearance of a pinned joint, this column-to-beam connection was designed as a semi-rigid joint that utilized the bolt spacing. This detail not only enhanced the transportability of the béquille and eliminated the need for on-site welding but also enabled the beam member to cantilever in two directions. It represents another dry construction detail typical of Prouvé’s designs, which were predicated on every component being prefabricated in a factory and assembled on site.
-
Photo (C) Centre Pompidou, MNAM-CCI Bibliothèque Kandinsky, Dist. RMN-Grand Palais / Fonds Prouvé / distributed by AMF
The most distinctive structural feature of the béquille was its pinned column base, secured by a single bolt, despite its overall asymmetrical form. In other words, a béquille could not stand on its own. If explained from a structural viewpoint, the béquille’s asymmetrical (unbalanced) cross-sectional form was aimed at generating a tension force on the V-column at its rear (north face), enabling it to stay upright like a balancing toy. This means that the north V-columns were designed not to bear the roof loads but to stabilize the béquilles. Properly understanding the structural system requires recognizing the béquille as working in conjunction with the tension element behind it as part of a two-component assembly, rather than as an independent support.
Similar to the specifications of the Prouvé House’s roof, the school’s roofs were constructed from 40-millimeter Rousseau panels that were formed into modules measuring 9,500 millimeters in length and 875 millimeters in width. However, unlike the house’s roof panels, which were joined using wood battens and bolts, the school’s panels utilized tongue and groove joints for a more seamless connection. The convex profiles of the roofs were formed simply by the way the central part of the béquilles pressed up against the Rousseau panels. Rather than spanning the full distance of about 6.6 meters from the center of the béquilles to the V-columns at the front (south face), the roofs spanned a reduced distance of 3.5 meters due to the presence of the long, cantilevered beams. Typically, a roof of this span, supported only by Rousseau panels, would necessitate tie beams to counteract wind loads. However, just as he did in his house’s roof, which spanned a similar distance, Prouvé omitted such cross-sectional structural elements, opting instead for a design that utilized the out-of-plane strength of the Rousseau panels to transfer the wind loads to the béquilles. In the longitudinal direction, the rows of V-columns and béquilles were linked together with steel channels (1C-100×50 and 1C-80×45, respectively), effectively stiffening the buildings in a manner akin to a rigid frame system.
-
Photo (C) Centre Pompidou, MNAM-CCI Bibliothèque Kandinsky, Dist. RMN-Grand Palais / Fonds Prouvé / distributed by AMF
In earlier iterations, the béquille resembled the wall frame with integrated storage shelves that Prouvé employed in his home. The approximately 600-millimeter-wide box-shaped frame would have been self-supporting, and it also would have been capable of creating the convex roof if given a slanted top. Moreover, all the V-columns were originally designed as vertical columns and, as such, were naturally intended to bear the axial compression forces from the roof load. Such a setup certainly would have made for an easier build; the realized design required the use of a gantry crane due to the instability of the slanted columns during construction and the weight of the Rousseau panels. In this regard, Prouvé deviated from his philosophy of designing components to be lifted and assembled solely by human strength. Why did he go so far to slant the V-columns? This can also be explained from a structural viewpoint. Assuming that the roof overhang could not be shortened, having vertical columns would have necessitated the Rousseau panels to span an additional 500 millimeters or so. This slight increase in length from 9.5 meters to 10 meters would have resulted in greater roof deflection, and consequently, the béquille would have tilted over further south, leading the building to experience greater story displacement from its own weight. Angling the columns inwards by a quarter span was thus a structurally grounded solution to enhancing the soundness of the building without compromising floor area. Revisiting the section drawings with this in mind, one could say that Prouvé’s attempt to create a structure that playfully addresses gravity while minimally impacting the land is very much in line with his characteristic tectonic design approach.
-
Initial and implemented sections
-
Roof deflection and story displacement diagram
The Afterlife of the Villejuif Temporary School
The buildings of the Villejuif Temporary School were dismantled in 1959, three years after construction, and their components were left stored at the site for a while. After cancelling its plans to reuse them, however, the City of Villejuif put the components up for sale at a price of 2,500 francs per classroom in 1967. Learning of this, Maurice Silvy, who had worked with Prouvé on the design of the Maison des Jours Meilleurs, acquired three modules (three former classrooms), or roughly 230 square meters of the original buildings, and repurposed them as his architectural office on Rue du Pasteur in the Paris suburb of Massy. Silvy also made a separate purchase of béquilles and donated them to the Musée des Arts Décoratifs in Paris, prompting an exhibition of Prouvé’s work the following year. The remaining classroom modules were sold to the commune of Quiberon in Brittany. Of these, two modules (two former classrooms) found their way to a private school and three modules (three former classrooms) were repurposed as a temporary chapel. While these buildings unfortunately were not placed under heritage protection, some of their components are preserved in the Musée National d’Art Moderne’s collection housed at the Centre Pompidou.
References
Ecole A Villejuif Près De Paris, L’Architecture d’Aujourd’hui, No.72, 1957
Peter Sulzer, Jean Prouvé: Complete Works: Volume 4: 1954–1984, Birkhäuser, 2008
Laurence and Patrick Seguin(eds.), Jean Prouvé vol.10: École Provisoire Villejuif Temporary School, Galerie Patrick Seguin, 2016
Reichlin, B. et al.: Jean Prouvé, TOTO Publishing, 2004.
Kochiku-no-Hito, Jean Prouvé, trans. Reiko Hayama, Misuzu Shobo, 2020.
DETAIL no.162, SHOKOKUSHA Publishing, 2004.
Shin Yokoo, Toshimasa Kobayashi, Jun Ishida, and Tatsuo Iwaoka, “Jan Purūve kenkyū: Sono 1: Tokkyo (patento) to kenchiku sakuhin no kankei” [Jean Prouvé research: I: The relationship between his patents and architectural works], Nihon kenchiku gakkai taikai (Tōkai): Gakujutsu kōen kōgaishū F-2: Kenchiku rekishi/ishō [Architectural Institute of Japan (Tokai Chapter): Summaries of Technical Lectures F-2: Architectural History/Design] (Architectural Institute of Japan, 2001): 609–610.
Top image: © Photo : Lucien Hervé, Paris
Shin Yokoo
Founded Ouvi in 2004 after completing a masterʼs degree in architecture at the Tokai University Graduate School of Engineering and working at the Masahiro Ikeda Architecture Studio. Earned a PhD (Engineering) from the Tokyo University of Science Graduate School of Science and Technology in 2016. Special lecturer at the University of Belgrade from 2017 to 2019 (one-year trainee of the Agency for Cultural Affairsʼ overseas study program). Visiting senior fellow at the National University of Singapore since 2020, Senior Lecturer from 2022. Visiting associate professor at the Tokyo University of Science from 2022. Notable works include the Matsumoto Sannomaru Square (2023; designed by Tatsuo Iwaoka Laboratory + MORIIS ATELIER), the MNH (2023; designed by ICU), the House in Nakago (2021; collaboration with Snark), 4 Episodes (2014; Atelier Nishikata), and Jukkaie (2009; collaboration with Point). Notable research includes “Design Feature of ʻMaison du Peuple de Clichyʼ Designed by E. Beaudouin, M. Lods, J. Prouvé”, (AIJ Journal of Technology and Design, Jun. 2015), “Study on the Relationship Between Features and Building Components of ʻAéro-Club Roland-Garros à Bucʼ” (AIJ Journal of Architecture and Planning, Jun. 2015), and “Study on the Relationship between Features and Building Components of ʻMaison démontable en ancier BLPSʼ” (AIJ Journal of Architecture and Planning, Sep. 2017), among others.
