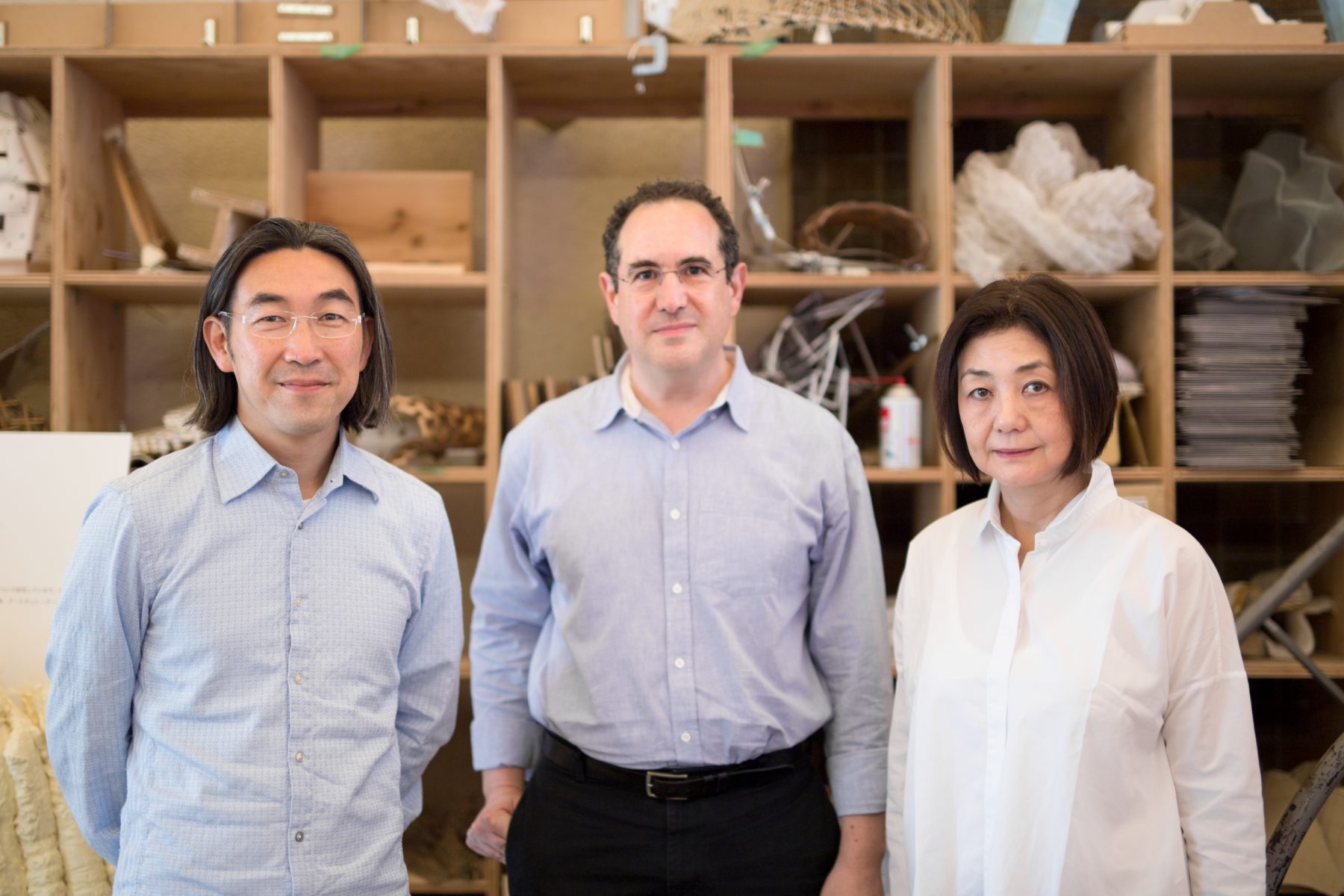
Series THE SAGA OF CONTINUOUS ARCHITECTURE
Architectural Intention behind Technology
27 Sep 2016
- Keywords
- Architecture
- Conversations
- Interviews
Reiser + Umemoto is the architect duo behind the design of the O-14 office tower in Dubai. What ultimately supported the realization of the complex architectural design that could only be developed with the help of the latest digital technology was an immense amount of manual work carried out by craftsmen on the construction site. In this interview, Associate Professor Yusuke Obuchi of the University of Tokyo delves into their thoughts on utilizing the power of both digital technology and engineering.
Yusuke Obuchi (hereinafter referred to as Obuchi): I’d like to discuss the O-14 project and the designing of windows and openings on the façade and the relationships.
Jesse Reiser (hereinafter referred to as Reiser): Rather than assuming that the building had an infinitely thin exterior boundary, even though it actually is in incredible sort of conflict with the environmental conditions of that area, it was a question. Around ten years ago an iconic structure having to have a reflective glass envelope and the environmental concerns of that were somewhat secondary issues simply because they could pump air-conditioning into the interior space to mitigate the problem.
With the initial design of O-14, we actually started with a more conventional curtain wall.
The first version of that building was, in a sense, more in line with a typical Dubai building. We had a very complex form outside and the windows actually caused a shift in the design because the geometry that we were proposing was so complex that it then became a problem in terms of how to get a curtain wall to work with it.
-
O-14 ©Reiser + Umemoto, RUR Architecture, D.P.C
Nanako Umemoto (hereinafter referred to as Umemoto): O-14 is a 22-story building and we used the same curtain wall details as an 85-story building with very complex forms, which we had designed previously. We used normative mullions and a glazing system.
Reiser: Right, but then our developer wanted essentially the same kind of formal characteristic of this very large 85-story building in a small 22-story building, so it then had to be translated into the geometry of the mullions and the framing.
Umemoto: But that’s not the only thing. If the building had been tall and large enough then you could have had this curtain wall system (because the curtain wall would have required its own structural system, and would have taken up a lot of space). But this building is small, so between its structure and curtain wall system, you don’t have space to occupy because you still have big columns going through.
Obuchi: Was there ever a possibility of integrating the structure and curtain wall system?
Reiser: Yes. I mean, in the end, we abandoned the curtain wall project, changed the form of the building to something much simpler, and then we decided to completely separate the glazing from the exoskeleton on the outside of the building.
Umemoto: In fact, we combined the structural system and the façade, but it’s a reversal of the normal building; glazing inside and structure outside.
Even though the geometry of the building is a straight projection, quite a complex curvature is applied, and because of its curvature, each opening is different.
Obuchi: But even before O-14, just looking through your past projects–The Sagaponac House, for instance–always looked interesting; there is a sense of play with openings, windows, structures and mullions. And the functions seem to overlap in order to produce a certain kind of visual effect.
Can you elaborate on that? The window is such a traditional architectural element, yet your windows are quite different.
Umemoto: If we had used a normal window system then we would have had to follow the system of slabs. But in the case of O-14, we reversed the system of the structure and façade, so the façade became the primary structure and not an environmental boundary.
Reiser: There was also a question of cost. We were able to use a much less expensive window wall that went from slab to slab rather than hanging off the façade. Then we could put all of our effort and finances into the exoskeleton, and not mix the two systems. Separating them was really a benefit in many respects.
We’ve always been interested in not simply a modernist notion of the building envelope as being infinitely thin and transparent, but in a certain kind of strange way it goes back to earlier notions of a façade architecture where we are dealing with multiple layers. For example, in the case of The Sagaponac House, there is a strange play between a more classical way of designing façades and signifying where the columns or supports are.
There’s also a play between a more symbolic use of columns to definitively create corners. Also, the rod system is actually doing the structural work. So, it’s a mannerist project. It’s a strange mannerist project.
Obuchi: Your projects produce multiple readings, interpretations, and experiences.
There is an assumption that all of those complex geometries can be produced and then assembled. But as you know, it’s not as simple as you might perceive it digitally. How do you approach the use of digital technology and how do you maximize its technological possibilities?
Reiser: There was always more of an architectural intention behind that technology; not to see the technology independently of some very strong ideas about what the architectural effects would be.
Umemoto: I-Beam, for example, is one of our old projects. When we designed it, the technology wasn’t so developed, so we never thought of these different kinds of forms or infinite variations of windows or things that didn’t exist at that time. But when it came time to do O-14 it had become possible.
-
O-14 ©Reiser + Umemoto, RUR Architecture, D.P.C
Reiser: Although, ironically, I think O-14 actually mixed technologies (and maybe this is more the reality in a building today). But it’s not a bad thing for the future either; having a somewhat ideological will to integrate everything.
On the other hand, if one is after certain effects, then maybe relatively old modernist technologies can be brought into the relationship with very new forms of construction and technology. It might work very well.
I think there was more of an ideological push to see everything totally integrated. It’s not necessarily always architecturally advantageous.
Obuchi: Considering the ease with which you can make a parametric model, it’s almost as if you can design any shape or any pattern possible, including window shapes.
Umemoto: Yes, but I think that even though the technology is so advanced that any form is possible, you really have to know how buildings are built, and you also have to know materials. So, that gives us ideas and also limitations, which are really good things. Once you know the limitations and how to deal with those limitations with materials and building systems and you know the techniques, then you can come up with a certain way of producing the variations of forms and patterns in systematic ways.
But the funny thing was that after we found out the variations for the openings on O-14’s exoskeleton façade were infinite, we fabricated all the Styrofoam concrete formwork for the openings in China, and they didn’t use a computer. They projected everything and drew everything by hand.
Reiser: They didn’t trust the computer models, so they did all of the projective geometry again by hand.
Obuchi: They traced it manually.
Reiser: Yeah, they had an army of guys projecting everything, so all of that work, from our side to automate fabrication using a computer was there, but it wasn’t used. They were too anxious.
Obuchi: But there are a lot of holes.
Umemoto: They did everything by hand.
Reiser: 1800 were done.
Obuchi: Wow!
Reiser: I think O-14 represents a certain moment in the history of technology and manual work. I am sure ultimately that that will go away, but it represents a certain moment.
Obuchi: Advancements in digital technology are developed with the assumption that everything can be produced with a great degree of precision and in a highly repetitive way. Yes, it’s economically possible because technology doesn’t really require any extra effort when making all those different parts, however, when those parts arrive at the construction site, it suddenly becomes an entirely different set of issues.
Umemoto: Well, that’s not really correct, because when you design things, even if they have infinite shape possibilities, everybody has to have ideas about construction techniques and material behavior. Concrete behaves differently from aluminum.
I am sure everybody has that in their mind, and therefore we know the limitations. As I said before, limitations are very important to know.
Reiser: A young Russian in my opaque seminar explored a radically fast and light mode of fabrication, even though traditionally, when talking about the opaque one assumes it is heavy and slow like stone. With this idea, a very complex thing might be fabricated that would have the lifespan of a piece of fashion and that you would keep making new throw-away iterations. You could keep making these things and creating architectures that might be very short-lived.
Obuchi: So, it’s an interesting spin-off of digital technology.
Reiser: Yes.
Obuchi: It’s not about the digital technologies and seeing what we can do with all these complex conditions. We conceptualized boundary conditions, and this is literal and phenomenal transparency.
-
O-14 ©Reiser + Umemoto, RUR Architecture, D.P.C
Reiser: Yes. The other part of this project which I want to mention is our collaboration with a really brilliant environmental technologist, Forrest Meggers, who joined our faculty at Princeton.
He sees everything in terms of their thermodynamic properties and actually is not among engineers who would seek to optimize building construction, but he actually utilizes heat flows to create certain effects and to create a kind of sustainable environmental condition for the building. He actually likes the idea of disfunction ─ that there is leakage, for example, he looks at the aluminum frames of the building, and sees that they may not be functioning optimally; they project heat or are pulling heat out of the building. He utilizes those.
Things that seem to be problems in terms of a way of creating an environmental condition are things he sees more as a realistic proposition. In a way, it’s very old.
Like the kotatsu in Japan. The heads of the people using it might be cool, but the kotatsu is warm. He is really interested in that and what materials can do, but he takes it to a highly advanced level of technology. So, we collaborated with him on our own competition for the Adidas Campus. He said most engineers today speak the rhetoric of collaboration from the beginning.
He said, “I don’t want you to do that. Please develop the design and advance it to a fairly high degree of definition. I’m sure it’s going to be loaded with environmental problems. That’s how I want to work through your building.” So it was a big flat floor plate with a lot of skylights. There were hot spots everywhere (which is an environmental no-no). He used both passive and active systems to move the heat flows around to generate air flow and do other things.
He actually likes using the imperfections rather than using an optimizing logic or a logic of trying to bring multiple factors together in the abstract. Both strategies were fascinating. I mean, it was also much more congenial to our way of working.
Obuchi: Does he think this is a better way to produce a project as an engineer?
Reiser: Yes.
Obuchi: Knowing exactly where the problem is and then developing it.
But it’s actually more work for you because then you have to do the project all over again to some extent.
Reiser: To some extent there is a reworking, yeah. But I think that’s a productive mode of working.
Obuchi: I suppose you agree upon certain things.
Reiser: Right. We’re agreeing to some kind of optimal condition, tabula rasa, and the abstract. And then trying to reach that goal.
Architecture will always be in some kind of conflict with the engineering. Unless you want to do it as an engineer. But there wouldn’t automatically be a consonance between an engineer’s agenda and an architect’s.
What I find so interesting is that for him it becomes a productive moment. I mean, it becomes a productive moment for both of us.
Obuchi: How much of that experience do you have in trying to bring some of those ideas back into teaching students? Or are academic exercises always trying to be more idealistic?
Umemoto: I don’t know about him, because I teach separately from Jesse, but my feeling is that if a student knows too much about how to put a window together, that creates a problem as far as really making interesting, original architectural ideas. I mean, that’s a really funny thing to say. I will push them to always be on the way to producing something. We will push the students to get it into more of a breakdown of the surface into a more abstract field.
If they simply have a surface without knowing what kind of field they are dealing with, then they end up putting in these window frames, and that’s a danger, right? We have to teach them how to really produce openings on the surface. So, before they get into that, we have to teach them how to tessellate the surface, for example, into certain finer scales of fields, or to have some kind of feeling about the materials.
Obuchi: Let me bring back the issue of the window. Should we look at the study of windows as purely practical applications, or are there other criteria through which we can study them? Has digital technology changed windows, or are there certain things that just don’t change? Or, if windows have changed, what are the kinds of things that have changed?
Reiser: I think digital technology enables certain traits of very traditional ways of producing fenestration or implementing boundaries. It goes beyond tradition because their thermodynamic performance can be tracked and amplified, resulting in an entirely new form of fenestration. Maybe in materials other than what the originals were.
-
“The Window is the Prime Mediator of Technology and Culture.”
Jesse Reiser + Nanako Umemoto
Jesse Reiser and Nanako Umemoto are the Principals of Reiser + Umemoto, RUR Architecture, D.P.C., an internationally recognized design firm. Prior to forming RUR Architecture, he worked for the offices of John Hejduk and Aldo Rossi. He is currently a Professor of Architecture at Princeton University, and has previously taught at Columbia, Yale, Ohio State, Cooper Union, and Hong Kong. Umemoto studied at the School of Landscape Architecture and Urban Design at Osaka University of Art before receiving her Bachelor of Architecture from Cooper Union. She is a Visiting Professor at Columbia, SCI-Arc, the University of Pennsylvania, the Pratt Institute, and Hong Kong University. Their firm received the 1999 Chrysler Award for Excellence in Design in 1999, and in 2000 Reiser and Umemoto Received the Academy Award in Architecture by the American Academy of Arts and Letters in 2000. They received the John Hejduk Award from Cooper Union in 2011.
http://www.reiser-umemoto.com/
Yusuke Obuchi
Born in Chiba Prefecture 1969. University of Toronto Department of Architecture 1989-1991. Roto Architects 1991-1995. Graduated Southern California Institute of Architecture 1997. Completed Princeton Graduate School Master’s Course 2002. RUR Architecture 2002-2003. Course Master, AA School 2003-2005. Director, AA School Design Research Lab 2005-2011. Instructor, Harvard Graduate School of Design 2013. Visiting Associate Professor, Princeton Graduate School 2012-2013. Project Associate Professor, The University of Tokyo 2010-2014. Associate Professor, The University of Tokyo 2015-present.
http://t-ads.org/
http://obuchi-lab.blogspot.jp/
MORE FROM THE SERIES
-
THE SAGA OF CONTINUOUS ARCHITECTURE
The Window Works at the Existential and Philosophical Level
02 Nov 2016
THE SAGA OF CONTINUOUS ARCHITECTURE
The Window is the Difference
between the Life and Death of a Space11 Oct 2016
THE SAGA OF CONTINUOUS ARCHITECTURE
“Why is This Guy Asking Me to Think about
the U-value and the Leakage?”06 Sep 2016
THE SAGA OF CONTINUOUS ARCHITECTURE
What Do You Think of Glass?
28 Jul 2016