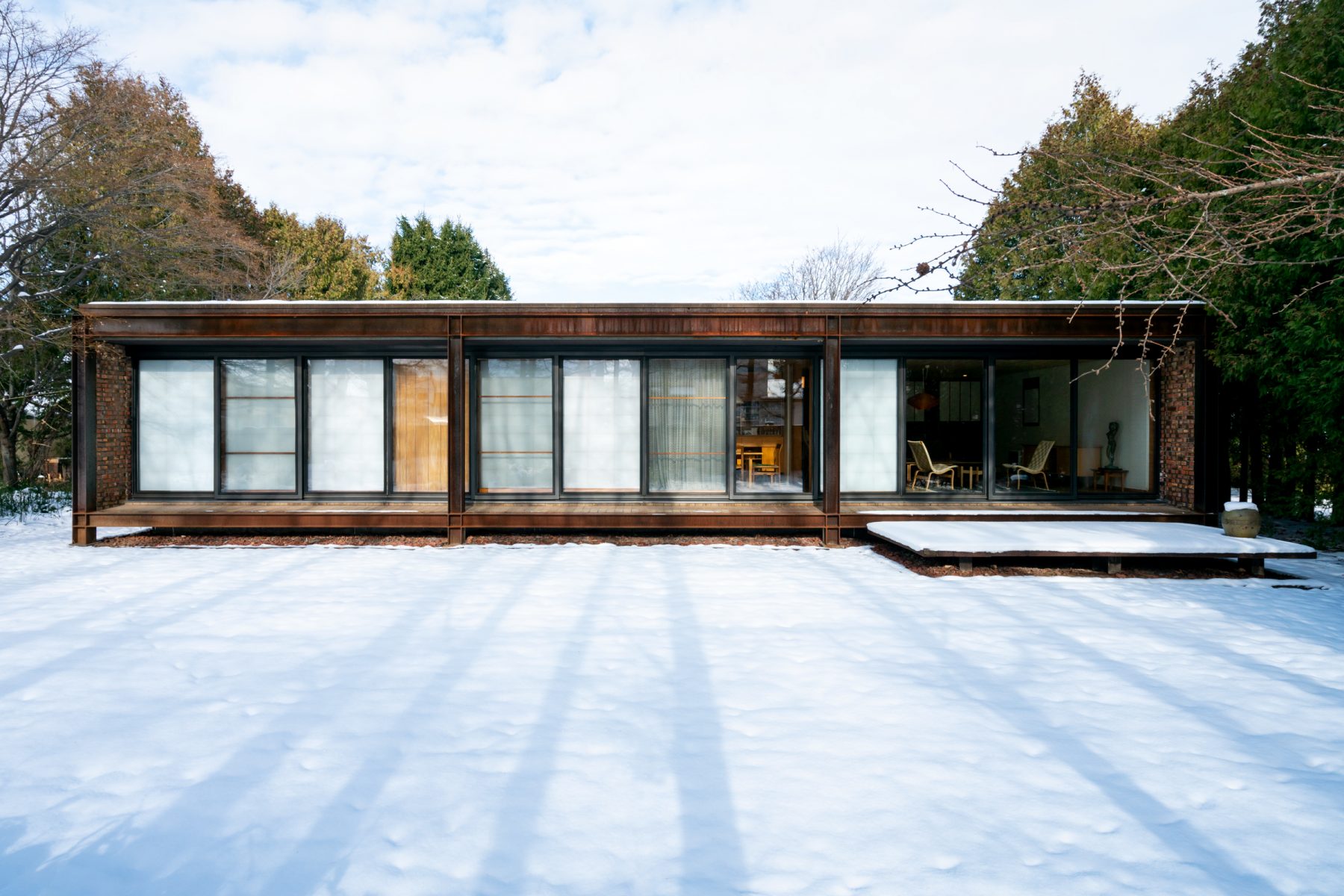
Series Windows of Japanese Modernist Architecture
The Experimental Design of the KATONO House in Sapporo
12 Apr 2023
- Keywords
- Architecture
- Japan
Known as an experimental work of modern architecture tailored for Hokkaido’s climate, the KATONO House (Personal Residence) in Sapporo designed by renowned Hokkaido architect Tetsu Katono (1924–2009) incorporated new building technologies such as curtain walls structured by a weathering frame, multi-layered windows, and a copper-pipe floor heating system, and fused them with vernacular design elements such as brick walls and shōji doors. How did Katono envision this prototype of north-country modernism? Takahito Miyagishima, a young architect based in Hokkaido, explains the experimental ideas manifested in the work.
The KATONO House is a single-story, steel-framed house that architect Tetsu Katono had built for himself in 1968 in what was at the time a beautiful agricultural area in the southern outskirts of Sapporo, Hokkaido. Standing amidst larch and cypress trees, the exquisitely proportioned house is composed beautifully of a weathering steel frame and brick walls. On its south side, an engawa [veranda] spanning the full length of the building faces the yard, and set back from its outer edge by about 800 millimeters is a 16.5-meter-wide ribbon window that is framed with black steel and backed by soft shōji [paper-covered lattice screens]. This “experimental house”, as the architect called it, incorporated the latest building materials and MEP systems of its time, and it continues to be looked upon as a beacon of Japanese north-country architecture to this day.
-
View of the house from the yard (south side).
Now, I would like to provide an overview of the housing situation in Hokkaido around the time it was designed. In 1953, 15 years before the KATONO House was completed, the Hokkaido Bokan Jutaku Kensetsuto Sokushinho [Hokkaido was enacted, marking a turning point for housing policy in the prefecture. The aim of this act that propelled the spread of non-wooden thermally insulated homes was to improve living conditions in Hokkaido while also promoting the rational use of the timber supply and advancing fire protection. The increased difficulty of getting mortgages on wooden houses sparked the popularization of the sankakuyane jūtaku [lit. “triangular roof house”], which were built with concrete masonry unit (CMU) walls and simple triangular roofs. Houses at the time were not usually built with insulation, and even when they were, the insulation consisted of nothing more than sawdust (glass wool was not used until the 1960s), while openings were made as double-layered windows composed of a single-pane, aluminum-framed window backed by an inner wood-framed window. In 1969, a year after the completion of the KATONO House, the Cold-Climate Housing Act was revised to specify thermal insulation standards, but general housing was still only required to have around 25 millimeters of glass wool. The number of wooden houses increased as mortgage qualifications were extended to include wooden and steel-framed houses, but as insulation and airtightness improved, a different problem worsened: condensation. It would take another 15 years or so for the causes to be identified, empirical research to be conducted, and know-how on measures for preventing condensation and controlling airflow in wall cavities, such as the implementation of vapor barriers, airtight construction, ventilation layers, and draft stoppers, to be disseminated.
Generally speaking, ambitious works of architecture aim to capture the spirit of the coming age. One can imagine how shockingly advanced the KATONO House must have seemed with its spaces framed with exposed steel, its double-glazed ribbon window, its hot water floor heating system, and its 100-millimeter-thick polystyrene foam insulation. The reason Katono employed a steel-framed structure was that he was inspired by the architecture of the Eames and Mies, and he also wanted to experiment further with steel-framed housing after having designed one for the first time in his previous job at the Takenaka Corporation. A steel-framed structure is prone to thermal bridging because of the high thermal conductivity of steel, and it also has a very high risk of producing condensation because of its low thermal capacity. It is thus a particularly challenging type of structural system to employ in cold climates as it requires the utmost consideration. Katono certainly would have been well aware of its risks, and yet he opted to explore its possibilities in Hokkaido’s cold climate. What was he looking to achieve?
-
The curtain wall realized with a steel frame made of weathering steel.
For one, a steel-framed structure can create large spans. It also makes flat-roofed designs possible because it has no problem with supporting snow loads. Furthermore, it releases the walls from the structure, turning them into curtain walls that also free the openings from constraints. Curtain walls can be flexibly configured with cladding, insulation layers, and ventilation layers according to the desired performance levels, and consequently puts a greater emphasis on the problem of how one should treat the materiality of the envelope. Katono adopted a double-wall system composed of an inner CMU wall and an outer brick wall with a ventilation layer in between, and he installed internal wall insulation using 100-millimeter-thick polystyrene foam boards, which were still uncommon at the time. The way that the curtain wall has been layered up, forming a thick envelope rather than becoming thinner, is a characteristic unique to the cold-climate region. Doing so had the effect of increasing the thermal capacity of the structure, making it more stable against changes in the outdoor temperature. Katono liked to use brick because it is a beautiful material capable of withstanding the harsh climate of the north. It was also a familiar material because bricks were produced nearby in Nopporo [an area known for brick production in the neighboring city of Ebetsu]. They were expensive, however, so he used unevenly colored reject bricks, which he was able to purchase cheaply. This was how his beautiful variegated brick walls with a half-artificial, half-natural feel came to be. The use of brick in structures had generally been avoided in Japan since the vulnerability of brick masonry structures was exposed by the Great Kanto Earthquake of 1923, but he brilliantly brought the brick wall back by turning it into a curtain wall. As if to highlight this fact, the brick walls of the house have been designed to not sit on the ground but rather float lightly above it on I-beams. In this way, Katono continued inventing solutions one after another through grappling with issues universal to the north country while using the steel-framed structure as a basic framework.
-
View of the entry porch. The structure on the right is a later addition (built 1982).
Katono’s bold experimental designs were supported by their details, which the architect cared for greatly, especially when it came to the windows. His ingenuity can be seen on full display in the openings that have been freed from the structure. If one includes the doors of the storage units, the interior is filled almost entirely with fittings and a rich variety of accompanying millwork. The large opening facing the yard is designed as a ribbon window composed of custom-made weathering steel sashes fitted with then-rare double-glazing of the maximum manufacturable size and large top-hung sliding doors that correspond to each one of the rooms. Compared to steel sashes, the aluminum sashes available on the market had higher thermal conductivity values and wider face widths, so Katano had pouch-like sashes fabricated with steel profiles and bent plates, and used gaskets to fit the glazing. The living room has a modest yet comfortable ceiling height of 2,300 millimeters, but the space feels cozier in person, having seemingly a lower center of gravity than one might expect from this measurement. This could perhaps be because the sashes have been positioned in such a way that only the gaskets peek from the edge of the floor, so you get a fine awareness of the space’s exquisitely calculated descent towards the engawa, the tsukimidai [lit. “moon-viewing platform”; i.e., terrace], and the yard beyond. Before I knew it, I found myself sitting on the high-quality furniture, gazing out to the yard in the winter sun.
-
The living room faces onto the tsukimidai.
As a general principle, to prevent the formation of condensation, one should avoid exposing materials with high thermal conductivity to the indoor air. The narrow face widths of the sashes are thus advantageous in this regard. It is also safer to expose the gaskets than the steel sashes. This is also the reason why Katono lined the inner side of the steel mullions with wood. The sliding doors are designed to be pulled with a handle positioned on the lower part of the sash and secured using a cremone bolt, which is a locking mechanism effective for improving airtightness. However, as there is a limit to how airtight sliding doors can be, they are paired with sliding shōji that are faced with washi [Japanese handmade paper] on both sides, acting as insulation doors. The air sandwiched by the washi creates a temperature difference of nearly 10 degrees Celsius between the inner and outer side of the shōji. At night, heavy curtains can be drawn to create an additional barrier against the cold. One can thus make fine adjustments to the indoor climate by smartly combining these four air barriers (between the double glazing, the windows and shōji, the double layer of washi, and the shōji and curtains). These adjustments always correlate with the behaviors of the people living in the house. For example, in the winter, one can leave the shōji open during the day to collect the solar radiation, close them before sundown to retain the warmth, and then cover them with the curtains at night. When there is less sun, one can leave the shōji closed and spend the day indoors in the hazy white light. While having a large south-facing opening does have its risks, it can be a powerful ally for homes in northern regions if one learns how to harness the sunlight. The shōji, in particular, are a feature that can be used to dramatically transform the feel of the interiors and one’s perceived sense of distance from the outside.
-
South opening (with shōji closed). -
South opening (with shōji open).
-
Detail of South opening.
The small windows on the east sides of the house are also emblematic openings with rich details. They are double-layered windows composed of an outer side-hung steel window and an inner wooden storm window. Both have ventilation grilles at the top, and there is a small wooden ventilation panel between them that can be operated from the inside. The storm window has a tiny knob that seems to say, “Please handle with care”. The grille is left open to let in the breeze in the summer, and it is also useful for exchanging the air during the winter. The handing of the storm window has been switched from the time when the house was first constructed. It is not clear whether this change was made because the windows were tricky to operate when their hinge sides aligned or because Katono wanted to preserve the blankness of the wall that backdrops the dining room. Perhaps it is a trace of his experimental process.
-
East window (closed). -
East window (open).
-
Exterior view of the east window.
At the entrance to the house, there is a large sliding glass door that separates the vestibule and hall. Both spaces have a double-layered window composed of a steel outswing window and a wooden sliding storm window, which are positioned symmetrically on each side of the glass door. The oversized pelmets concealing the curtain rails above these openings cause a scale shift that tightens up the space, giving it the same cozy feel as the living room. And here, too, the combination of the outswing windows, sliding storm windows, and curtains create a rich variety of expressions that change with the seasons and time. The windows and their accompanying elements constitute the entire wall design.
-
Entrance hall window (with storm window closed). -
Entrance hall window (with storm window open)
-
The sliding glass door between the entrance hall and vestibule.
Katono opted not to use double glazing in his studio that he built on the same site as his home in 1992, instead adopting a layered window system composed of two single-pane windows with a somewhat wide ventilation layer in between. Large double-glazed windows are difficult to replace if, for example, the seals degrade and the insulating gas leaks, allowing air to penetrate the gap and cause internal condensation. Katono thus shifted to using layered single-pane windows when designing large openings in consideration of future maintainability. It is truly admirable how he was still engaging the problems of double glazing and experimenting with ways of overcoming them even after 24 years from when he first adopted them in his own house. Even now, a fundamental solution to the problem of internal condensation caused by the deterioration of double-glazing systems has yet to be found.
The history of settlement in Hokkaido was a history of resignation, particularly in terms of living practices. In the face of the unforgiving climate, the tondenhei [soldiers recruited to settle Japan’s northern frontier in the late 19th century] who arrived from all over the country had to let go of many of the architectural styles, lifestyles, and customs that they brought with them from their homelands. This should be no surprise considering that they were virtually transplanted from a monsoon climate to a subarctic climate. The objective of the settlement of Hokkaido was to modernize the undeveloped territory in the shortest time possible. For architecture, this entailed importing advanced technology and know-how from foreign northern-latitude cultural spheres and making use of what was on hand to develop a specifically Hokkaidoan architecture and culture. To express this positively, one could say that Hokkaido offered a field for experimenting freely with few constraints. To my mind, the pioneer mentality ingrained in this land does not seem unrelated to Katono’s boundless spirit of experimentation. When Katono speaks about striving to realize a type of housing that is appropriate for Hokkaido, one can catch glimpses of this land’s history in his every word. And to this point, he composed the KATONO House mainly with industrial products and natural materials that were readily available in Hokkaido at the time, such as weathering steel from Muroran, double glazing from Sapporo, and brick from Nopporo. The wood veneer that he used for the interiors was also a Hokkaido-made product manufactured to be exported overseas, and the Kalopanax and Japanese oak wood that he used are native hardwoods. Thus, another important theme of the KATONO House was to create a locally-rooted architecture in an inexpensive way, and it was from within this constraint that his innovative detailing and inventive use of materials emerged.
-
Exterior view of the south side.
Katono continued to experiment with steel-framed housing based off the KATONO House for more than a quarter century, producing a wide variety of designs along the way. One can find many hints for designing houses suited to Hokkaido throughout them, such as the idea of using pilotis to lift the living room to the second story, creating beneath it a sheltered approach or a semi-outdoor summer terrace that is unaffected by the weather. Katono’s north-country modernism was a grand project to create, through responding to issues that are universal to cold-climate regions, housing that resynthesizes and reestablishes the various cultures, lifestyles, behaviors, and customs that the people of Hokkaido had once given up. Serving as a prototype for them all, the KATONO House still to this day continues to face us with many questions.
Takahito Miyagishima
Born 1986 in Hokkaido, Japan. Completed the master’s program in architecture in the Department of Civil and Environmental Engineering at the Tokyo Institute of Technology Graduate School of Science and Engineering in 2011. Studied as a scholar at the Higher Technical School of Architecture of Madrid (ETSAM) during the same year. Founded Takahito Miyagishima Architects in 2013. Withdrew (ABD) from the doctoral program at the Hokkaido University Graduate School of International Media, Communication, and Tourism Studies in 2018. Major works include Thoroughbred Farm (2016–), O Project (2020), and Rice Warehouse of Niidahonke (2022).
MORE FROM THE SERIES
-
Windows of Japanese Modernist Architecture
The Windows of Tomoya Masuda’s Naruto Cultural Center: A Faintly Bright Louvered Space
17 Jun 2025
Windows of Japanese Modernist Architecture
A Culmination of Sutemi Horiguchi’s Aperture Designs:
The Tokoname City Municipal Ceramics Research Institute (Tokoname Tounomori Research Institute)15 May 2025
Windows of Japanese Modernist Architecture
The Diversity of Windows in Kiyonori Kikutake’s Serizawa Literary Center (Serizawa Kojiro Memorial Museum)
25 Dec 2024
Windows of Japanese Modernist Architecture
The Windows of Hiroshi Hara’s Awazu House: Spaces of Light Illuminating the Darkness
26 Apr 2024