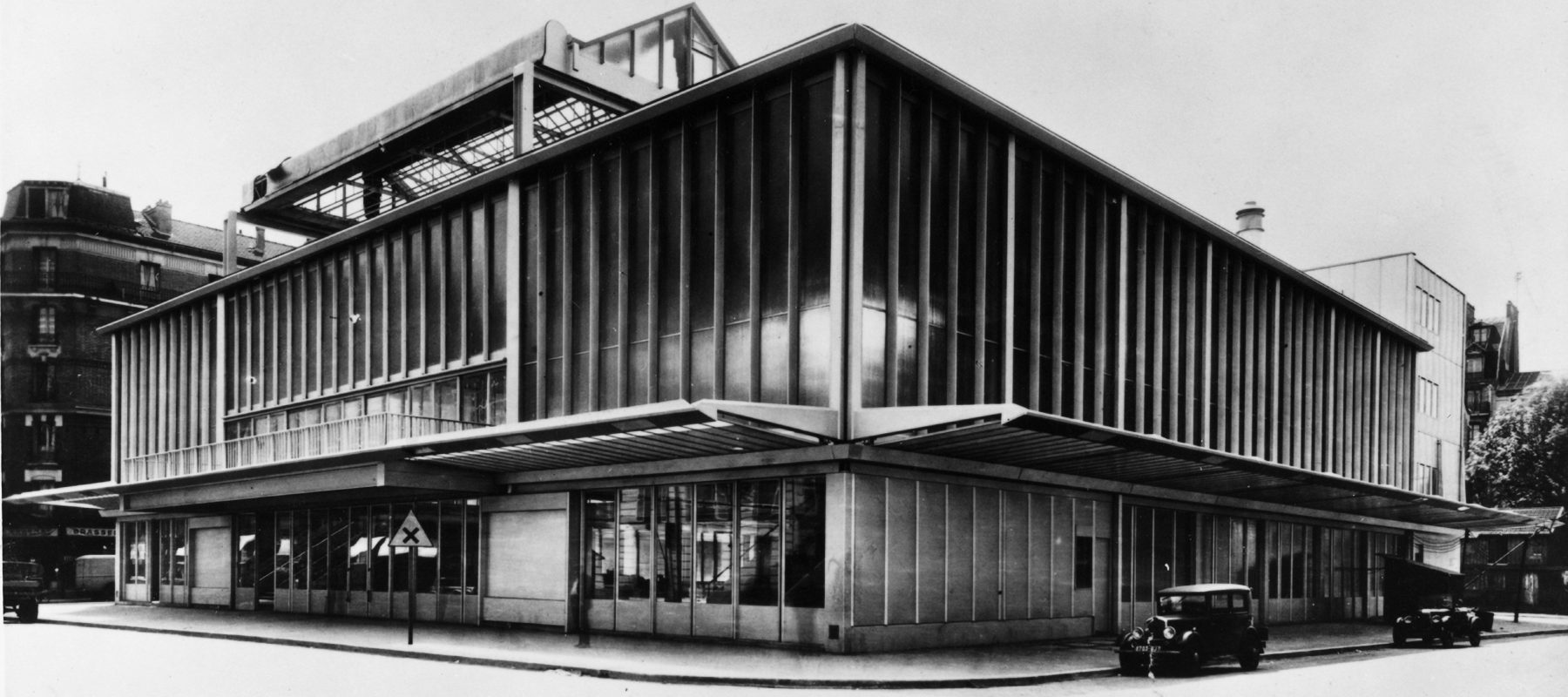
Four Tectonic Features that Reside Within Prouvé’s Window Details
04 Aug 2021
Jean Prouvé was originally a metalworker by trade, but he became a leading modernist architect himself through collaborating with progressive architects such as Le Corbusier. He is particularly known for making inventive use of industrial prefabrication from the postwar reconstruction years and demonstrating the possibilities of the new technology for not only architecture but also furniture design. In this article series, structural engineer Shin Yokoo, who has been researching Prouvé’s achievements from both an engineering and design perspective, sheds light on the architect’s experimental work with windows.
Jean Prouvé was born in 1901 in Nancy, France, and he went on to produce a great number of designs (primarily furniture and buildings) during his lifetime. Influenced by his father, Victor, who led an Art Nouveau school in Nancy, Prouvé took an apprenticeship with Émile Robert and began his creative career as a metalworker. In his late years, he headed the jury of the architecture competition for the Pompidou Center in Paris and contributed greatly towards its realization before he passed away in 1984. In the time between, he continued to actively collaborate with architects and his associates and experiment with new technology and construction methods as he produced design after design for projects that included pre- and post-war mass-producible temporary housing, private homes, public facilities, school buildings, and the furniture to go inside them. He carried out much of this work at his personal factory, Ateliers Jean Prouvé (founded in Nancy and later relocated to Maxéville), which was staffed by some 250 skilled workers. All told, he was involved in 1,456 projects, and 412 of them were architectural.
-
Jean Prouvé.
In these articles, I will be tracing the development of Prouvé’s thinking regarding the many experimental exterior wall and windows that he designed. To start, I will focus on one of his well-known furniture pieces and two of his characteristic architectural projects that have clearly delineated components while documenting the various ideas that he built into them through the use of axonometric drawings.
A Demountable Chair
Prouvé first came to be known for his original furniture designs that commanded high prices and attracted many collectors. One piece that held special meaning for him was the Standard Chair, which he continued to modify from 1934 to 1980 while changing its materials from steel to wood and then to aluminum, but never finished during his lifetime. It was special because he used it as a prototype for developing his architectural work.
-
Two chairs on far right: Early versions of the Standard Chair made with steel legs and molded plywood (1934). Third from right: Wooden version made in 1942. Fourth from right: Demountable version made in 1947. Fifth from right: 1950 was a bountiful year. This one is a demountable version made with wood. Sixth from right: Version with steel legs and sheet aluminum (1950). Seventh from right: Version with steel legs and faux leather upholstery (1950). Eighth from right: Near-finalized design made with steel legs and molded plywood (1950), just like the earliest versions. Far left: Prototype of a new model with aluminum back legs (1980). It was the last one that Prouvé worked on (it never reached the market because the manufacturer went out of business). Aluminum ribs were added along the inner side of the back legs to take full advantage of the material’s strength potential.
© Pen, 2002
The Standard Chair’s distinctive back legs are similar in form to the structural members that Prouvé designed for his buildings, and the progression of its materials from steel to wood to aluminum also aligns with the evolution of the materials that he built with. The version made in 1947 is particularly noteworthy, as it was the first one that could be taken apart and put back together again (i.e. a demountable chair), and it also marked the point where the basic design was more or less set. Prouvé made its components to be exchangeable with those of other Standard Chair models to lower its cost, and he devised ways to make it easy to assemble and disassemble—ideas that could also be applied to buildings—in order so that it could be exported to places such as Africa. These ideas included making the legs, seat, and backrest as independent components that are joined with bolts and hooks so that they can be easily assembled (or disassembled) on site.
-
Exploded drawing of a demountable Standard Chair.
A Pioneer of the Industrial Curtain Wall—The Maison du Peuple of Clichy
Prouvé worked on a full building from design to construction for the first time in 1938 through collaborating with French architects Eugène Beaudouin and Marcel Lods. That building was the still extant Maison du Peuple of Clichy in Paris, whose façades made using exterior mullions and curved metal exterior panels represent essentially the world’s first industrially prefabricated curtain wall systems ever implemented. I wrote “essentially the world’s first” because there are earlier examples, such as those of Walter Gropius’ Bauhaus Building (1926) and Leendert van der Vlugt and Johannes Andreas Brinkman’s Van Nelle Factory, which, though not completed until 1931, was designed before Gropius’ building. However, they had rudimentary details that relied on fillet sealant to attach the glass to the steel frames. As for the curtain walls of Ludwig Mies van der Rohe’s Lake Shore Drive Apartments, they were not built until the 1950s, and they were not fully prefabricated.
-
Maison du Peuple (exterior view from north).
One of the Maison du Peuple’s two types of curtain walls is composed of glass panes and mullions, as most curtain walls commonly are today. The mullions are set on the exterior side of the glass at intervals of 1.04 meters, and they are each composed of a pair of L-angles and four components made of folded sheet steel 1.8 millimeters thick. These mullions, which simultaneously hold in place the sashes of the clear glass front and the corrugated screens attached to the interior side, represent one of the many multifunctional components that Prouvé went on to develop. In their initial design, the mullions were given sectional curvature to compensate for the sheet steel’s lack of rigidity, but they were ultimately formed like standard sash profiles due to fabrication issues.
-
Exterior mullion designed with minimal components.
The second curtain wall is composed of three kinds of curved metal panels: panels with no openings, panels with windows, and panels with doors. Each panel is made of two folded pieces of 1.5-millimeter-thick sheet steel, and like the exterior mullions, they form façade modules with a standard width of 1.04 meters. Taking into consideration the need for the metal panels to be replaced in future repairs, Prouvé limited the weight of each to 90 kilograms and designed them so that they can be switched out from the inside using basic lifting equipment. The latter is achieved by a simple detail called the “hanging system”, which consists of a set of attachments at the top corners of the panels that hook onto the building structure. We can see from the way Prouvé approached the design of these panels that he extended his ideas for making the Standard Chair easy to assemble and disassemble, and his solution that allows these building components to be replaced also happens to be very much in line with current ecological and sustainable design thinking. Another feature to note is the use of curvature. Although the idea was scrapped from the design of the exterior mullions, it plays an important role in these panels. An internal array of springs in the central part of the panels gives the thin metal surfaces a slight convexity that enables them to stand on their own. Meanwhile, the side edges of the panels curve in the other direction to form beak-like ridges that prevent rainwater from penetrating the joints between the panels. The gaps along these joints are designed not only to serve as vents that help regulate the indoor temperature but also to absorb the temperature-induced expansion and contraction of the metal panels.
-
The curved metal exterior panels are both robust and beautiful.
The Maison du Peuple was designed for three purposes, and it was used differently throughout the day. In the morning it was a market (lower and upper floors), and in the afternoon it became an assembly hall or a cinema (upper floor). This was made possible by three operable mechanisms: a glazed roof, sliding partitions, and retractable floor. The most distinctive of these features is the enormous electrically powered roof, which measures 17 meters by 17 meters in plan, has a sawtooth profile, and is equipped with 480-millimeter-diameter steel wheels that allow it to be rolled open on rails to create a direct connection to the sky.
RESONANT ARCHITECTUR
Conception: Nicolas Maigret, Nicolas Montgermont, Jeremy Gravayat, Yann Leguay
Info: resonantarchitecture.com
When the building was used as a market in the morning, the glazed roof and retractable section of the upper floor were rolled back to create a partially open-air mezzanined space, which was better suited for using the two levels in an integrated manner as well as for dissipating the smell of the food products. In the afternoon, the upper floor could be quickly turned into a well-lit assembly hall by rolling the roof and retractable floor back out again. When it was used as a cinema, sliding partitions and ceiling-hung blackout curtains were pulled out to turn the central area of the floor into a dark screening room. This is also the reason why the building’s curtain walls were designed to be transparent at the front but opaque at the back.
Owing to the fact that the building stood through the Second World War, it had to be repaired several times, and it also went through an unfortunate period of disuse. However, after being recognized as a historic landmark in 1983, it underwent restoration work from 1995 to 2005, and all of its once rusty mullions and panels were replaced.
Shape-Shifting Windows—The Building at Square Mozart
Despite what Prouvé accomplished at Clichy, his factory suffered financially because he was unable to recover more than half the project’s construction costs. This was what led him to seek funding from Aluminium France and Pechiney—two major companies that had been looking to grow the market for construction-use aluminum at the time—and he managed to not just maintain but expand his factory as a result. However, while this decision opened him up to the possibilities of aluminum, it also brought about the greatest misfortune of his life, as he would end up letting go of the factory upon completing the Building at Square Mozart.
-
The Building at Square Mozart.
Photo © Centre Pompidou, MNAM-CCI Bibliothèque Kandinsky, Dist. RMN-Grand Palais / distributed by AMF
Standing in a quiet neighborhood in the 16th arrondissement of Paris, the Building at Square Mozart (known in French as the Immeuble de Logements Square Mozart) emits a unique presence even today. This can be attributed to the building’s façade, which Prouvé realized through collaborating with Lionel Mirabaud in 1953. For it he developed an operable window system that capitalizes on the qualities of lightness, strength, and malleability that aluminum offers.
-
The operable window system has six different modes.
Three different operable mechanisms have been integrated into the façade panels, which are made of 0.8-millimeter-thick corrugated aluminum sheet and form 1.45-meter-wide by 2.63-meter-tall modules. In the top section of the panels, there is a transom with small round ventilation holes that slide open horizontally. The middle section holds a vertical sliding glass window equipped with a balance so that it can be set freely at any height. The final and most intriguing mechanism is located in the bottom section. It is composed of a vertical sliding aluminum shutter attached to a thermally insulated wall element.
-
Sash and mullion details.
When lowered the shutter acts as a ventilation grille, and when raised it serves as a storm shutter. It can also be propped out to form an awning. These components moved smoothly when I tried them out in person, and I barely even felt the weight of the glass. Owing to Prouvé’s use of technology that allows the simple objects to be reconfigured in various ways, here the residents live together with the building façade, which continues to change its appearance over the course of the day and year as they raise, lower, and prop up their windows based on the weather and their mood.
-
The still working system of operable windows. (photographed in 2017)
© Kazuki Horikoshi
Four Tectonic Features of Prouvé’s Windows
An important aspect of Prouvé’s work lies in the way he constructed the relationships between materials, or in other words, between one part and another. One could say that he designed his furniture and buildings from the parts up through a tectonic—or technologically inspired—approach while drawing inspiration from the production equipment and materials in his factory. The following are four tectonic features that can be identified in his window designs: (1) methods that allow for easy assembly and disassembly, (2) operable mechanisms, (3) components that serve multiple functions, and (4) technology that allows simple objects to be reconfigured in various ways. These features are manifested through Prouvé’s details as unique building parts that behave autonomously from the whole. Looking at his work it almost seems like he was out to prove that industrialized construction does not necessarily equate to design monotony, and that if anything, it should be embraced as a means for achieving design diversity. Indeed, I have little doubt that this was a conviction he maintained throughout his career.
References
Reichlin, B. et al.: Jean Prouvé, TOTO Publishing, 2004.
Kochiku-no-Hito, Jean Prouvé, trans. Reiko Hayama, Misuzu Shobo, 2020.
Yokoo, S., Yamana, Y., Iwaoka, T.: Design Feature of “Maison du Peuple de Clichy” Designed by E. Beaudouin, M. Lods, J. Prouvé, AIJ Journal of Technology and Design, 21(48); 853-858, June 2015.
Yokoo, S., et al.: Study on Jean PROUVE, Part 2 : System Design, Summaries of Technical Papers of Annual Meeting, Architectural Institute of Japan, F-2, History and Theory of Architecture, 2001; 611–612, July 2001.
DETAIL no.162, SHOKOKUSHA Publishing, 2004.
Shin Yokoo
Structural engineer, born 1975
Founded Ouvi in 2004 after completing a masterʼs degree in architecture at the Tokai University Graduate School of Engineering and working at the Masahiro Ikeda Architecture Studio. Earned a PhD (Engineering) from the Tokyo University of Science Graduate School of Science and Technology in 2016. Special lecturer at the University of Belgrade from 2017 to 2019 (one-year trainee of the Agency for Cultural Affairsʼ overseas study program). Visiting senior fellow at the National University of Singapore since 2020. Notable works include the House in Nakago (2021; collaboration with Snark), 4 Episodes (2014; Atelier Nishikata), and Jukkaie (2009; collaboration with Point). Notable research includes “Design Feature of ʻMaison du Peuple de Clichyʼ Designed by E. Beaudouin, M. Lods, J. Prouvé”, (AIJ Journal of Technology and Design, Jun. 2015), “Study on the Relationship Between Features and Building Components of ʻAéro-Club Roland-Garros à Bucʼ” (AIJ Journal of Architecture and Planning, Jun. 2015), and “Study on the Relationship between Features and Building Components of ʻMaison démontable en ancier BLPSʼ” (AIJ Journal of Architecture and Planning, Sep. 2017), among others.
